Ultrasonic Welding Spotlight: How Weldmetrix is Revolutionizing Quality Assurance
Welcome to the world of ultrasonic welding, a field where precision and reliability are not just aspirations, but requirements. Enter the Weldmetrix MCRFN Acoustic Monitoring System, which captures the sound emitted during the welding process at an impressive sampling rate of 50 kHz. But why is this important?
The principle of the system is simple but powerful: if the process parameters remain constant, the sound emission will also remain constant. Changes in the sound emission are an unmistakable sign of irregularities in the process. Mathematical algorithms are used to analyze the noise behavior, and the system evaluates errors and irregularities according to the parameterized requirements of each application. In other words, the more stable and reproducible the process, the more accurate the quality assessment.
In a recent test setup, a two-channel application was used. Two microphones of the same type were positioned from different sides and with different angles of attack. Interestingly, the microphones were sampled at 50 kHz and the recorded signals were evaluated independently. An amplifier and an AD converter module were also used, and all parameterization and visualization was controlled by test software on a Weldmetrix technician’s laptop. A „high runner“ was used for the tests, a 5-pin connector consisting of two parts welded together with a Branson 901 ultrasonic welding machine. The parts were loaded manually, but there are plans to automate this step in a future production line. The tests themselves were performed using the Weldmetrix system’s auto trigger, a feature normally used only for testing. In production, a digital trigger is used to ensure that all data is recorded.
The Weldmetrix MCRFN system is not just another tool in the quality assurance toolbox. It is a paradigm shift that fundamentally changes the way we think about ultrasonic welding and quality assurance.
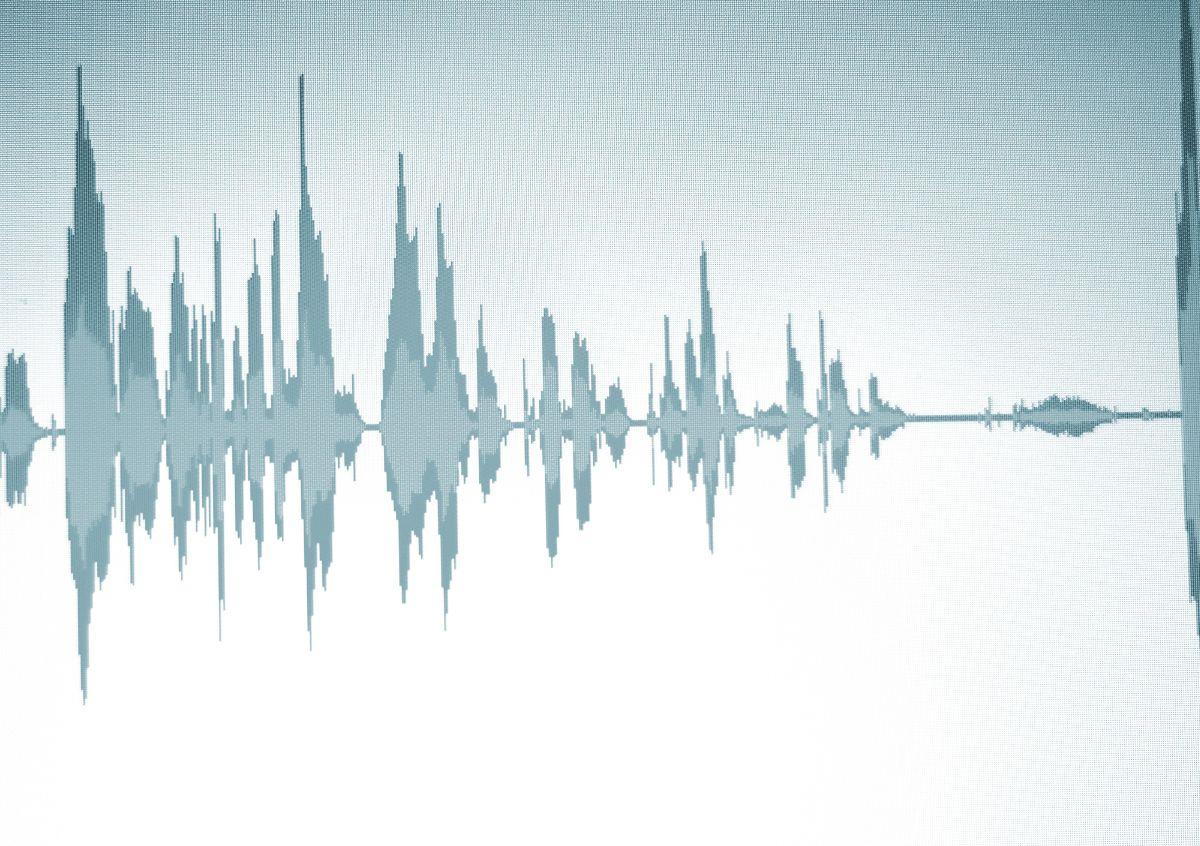
Test results: A look behind the scenes
The series of experiments with the Weldmetrix system has led to some remarkable results. First of all, it must be emphasized that Weldmetrix is a comparison system and not a measurement system. In the beginning, OK (In Order) reference welds were welded to provide a basis for evaluation. Then NOK (Not in Order) parts were produced by changing the process parameters such that the resulting parts did not meet the minimum breaking strength of 450 N.
Interestingly, the evaluation showed that changing the process parameters did not necessarily result in an NOK part. The Weldmetrix system correctly identified these changes in many cases, even though the part passed the fracture test. For parameterization, all reference welds were declared OK and all provoked test parts were declared NOK. The automatically set limits proved to be very reliable.
A special case was part 27, which was evaluated as NOK. For this part, the channel 0 signal in the last part of the weld was above the limits for all four algorithms. Component 47, on the other hand, was evaluated as OK, although the auto trigger did not work correctly and the beginning of the signal was not recorded. Another interesting example is component 91, which had a below-average breaking force. It is clear from the graphs that this measurement is significantly longer than the reference signals.
A total of five components were welded without foil. Four of these were rated OK and one was rated NOK. These results underscore the ability of the Weldmetrix system to detect and correctly evaluate even subtle changes in process parameters. The test series not only confirmed the reliability of the Weldmetrix system, but also demonstrated its ability to account for a wide range of process variables. This is another step towards more accurate and reliable quality assurance in ultrasonic welding.
Conclusion: The Art of the Right Angle and the Reliability of the Weldmetrix System
The experiments have impressively shown that the angle of attack of the microphone plays not only a minor but a decisive role in the quality of the signal processing. Although a larger angle of attack (CH0) allows for the detection of a broader error spectrum, it also has its limitations. Therefore, the combination of two different angles of attack is not only a good idea, but almost a must in order to exploit the full potential of the system.
In terms of parameterization, only OK reference sutures were used for automatic limit setting. This proved to be a wise decision, as all components with insufficient or below-average tensile strength were reliably detected by the Weldmetrix system. The measurements that held up despite changes in process parameters were deliberately not used for parameterization. This underscores the accuracy and reliability of the system.
Overall, the results confirm the excellent ability of the Weldmetrix system to reliably detect a wide range of defects and irregularities. This is another milestone on the way to more efficient and reliable quality assurance in ultrasonic welding. The journey continues and we can look forward to the next innovations.
weldmetrix GmbH
elevating standards, monitoring success
Headquarter
Gutheil Schoder Gasse 17
Techpark Vienna
1230 Vienna
Austria
Copyright © 2023 – weldmetrix GmbH