Quality assurance for welding processes
for welding processes
In the highly competitive and ever-evolving world of manufacturing and production, quality and efficiency are more than just competitive advantages – they are critical success factors.
In welding, in particular, the quality of a single weld can have a significant impact, ranging from failures and lost productivity to dramatic safety risks.
As a result, process monitoring is not an afterthought or an optional extra, but a critical element of quality assurance and a central factor in a company’s overall success. It is the tool that suppliers and manufacturers need to ensure that their joining processes always meet the highest quality standards.
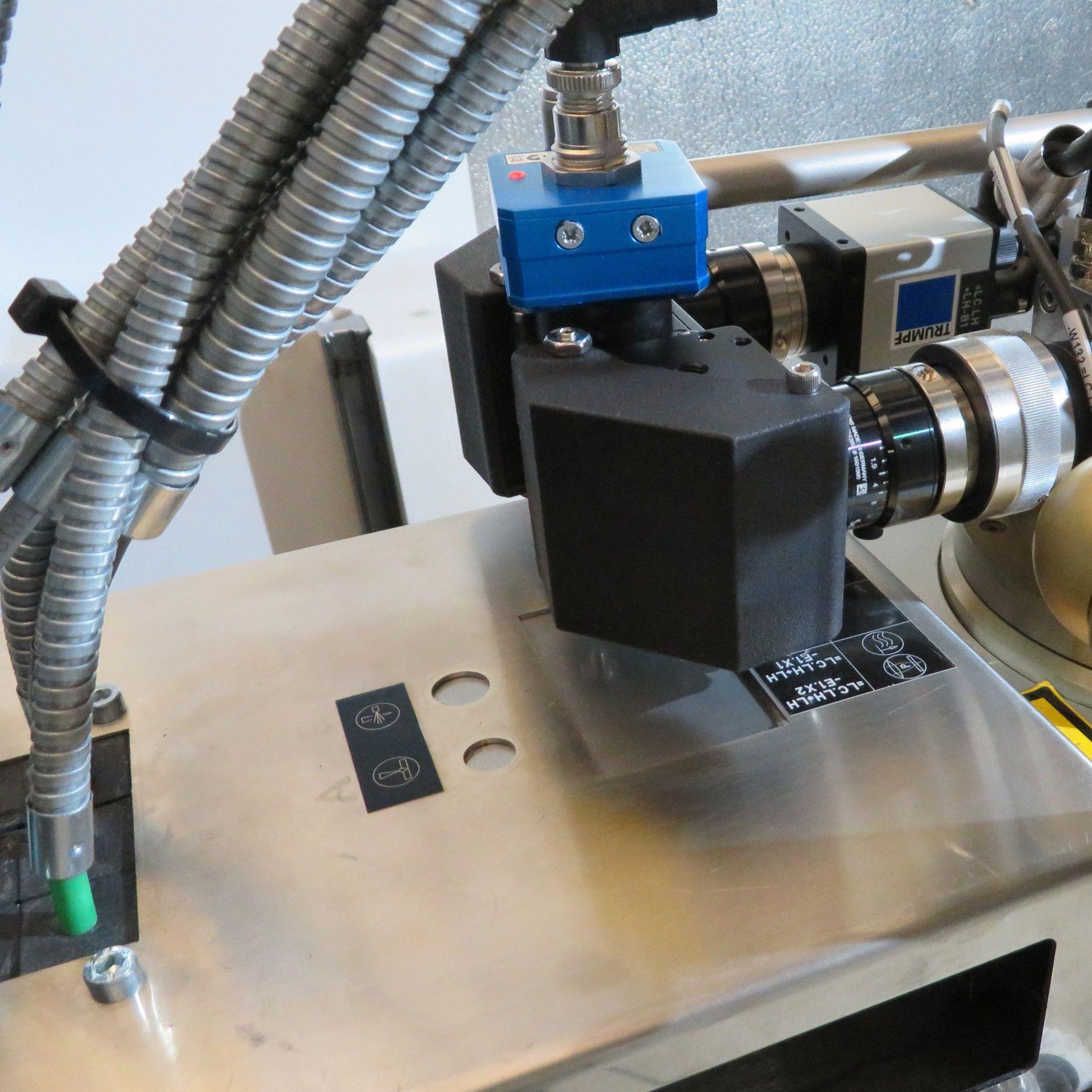
With effective process monitoring systems, companies can control every aspect of their joining processes, identify potential problems early, and make continuous improvements to ensure product quality. This is not just a nice-to-have, but an absolute must-have in the modern manufacturing landscape.
It is critical that you recognize the benefits of process monitoring and proactively implement it into your welding processes. Not only will it help you ensure the quality and efficiency of your production, but it will also build customer confidence by demonstrating that your processes meet the highest quality standards. We are here to help, with solutions tailored to your specific needs. Discover the possibilities that consistent process monitoring can bring to your business.
Effects of missing
Quality Management
Without effective quality management, companies face significant risks that go far beyond product defects. First, product quality may be inconsistent or inadequate, resulting in increased returns, warranty claims, and, in the worst case, product recalls. These problems can cause significant financial loss and business disruption.
Second, a lack of quality management can lead to an erosion of brand image and customer confidence. In a world where customers have access to extensive product information and reviews, a chain of quality problems can quickly lead to a loss of market share and reputation.
mehr lesen
Third, the lack of a quality management system can cause companies to miss important opportunities for improvement. Without systematic monitoring and analysis of quality data, companies cannot effectively learn, improve and innovate. This can ultimately hurt a company’s competitiveness and cause it to fall behind while competing companies that practice quality management move forward and thrive.
Finally, there can be legal and regulatory consequences if a company’s products do not meet government or industry quality standards. This can result in fines, penalties and, in extreme cases, shutdown of operations.
In short, the lack of quality management can seriously jeopardize a company’s financial health, brand image, customer relationships, continuous improvement capabilities, and regulatory compliance.
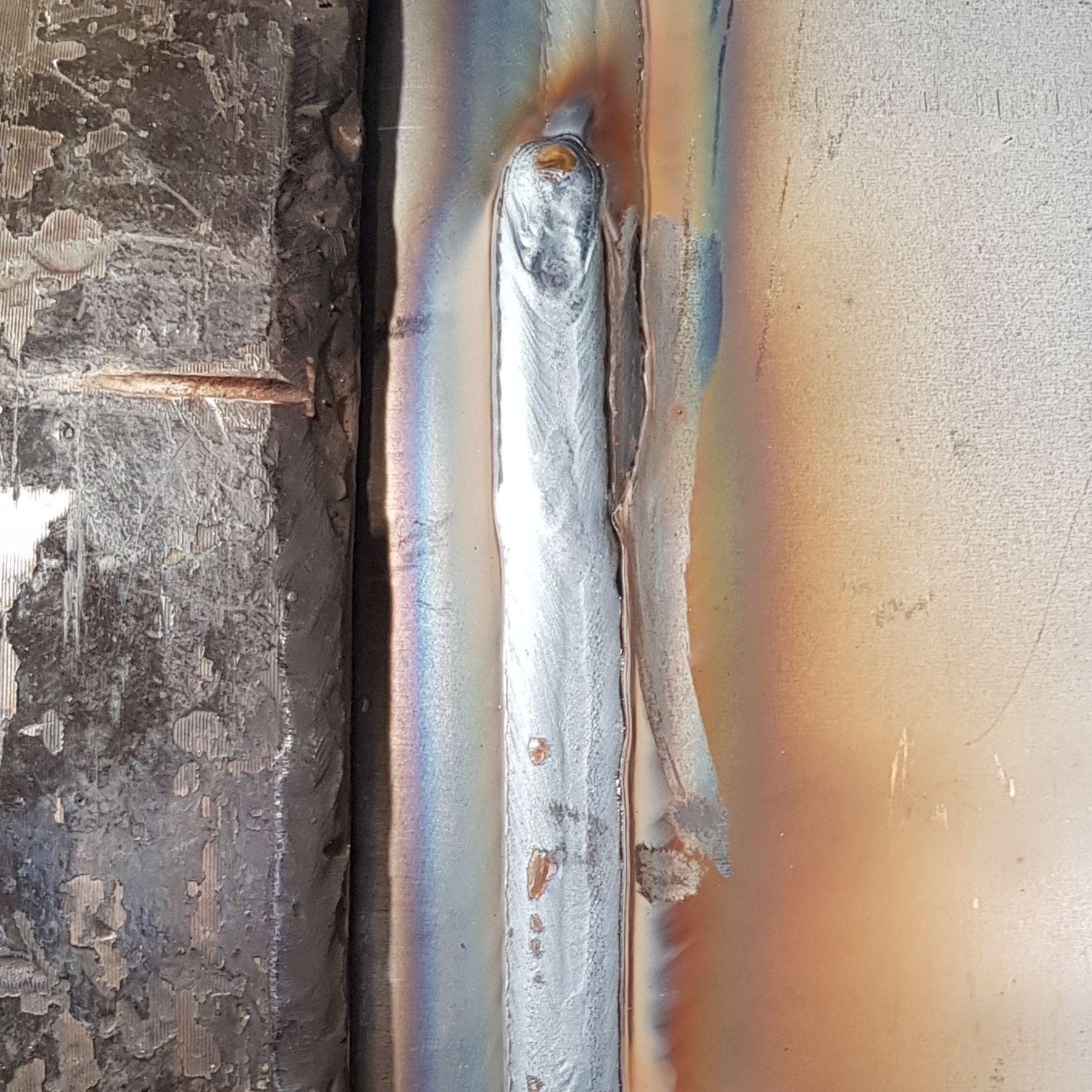
How do defective
welds occur
Welding defects occur for a variety of reasons, often related to materials, equipment, process and people.
Inaccuracies in material preparation or selection can result in incompatibility or lack of bond.
Faulty equipment or improper maintenance can lead to inconsistencies in welding speed, which can affect weld quality.
The MIG/MAG Process
itself can be significantly influenced by the following varying parameters
- current
- voltage
- speed
The Laser welding Process
can be significantly influenced by the following varying parameters:
- seam geometry
- laser power
- material properties (contamination)
The High-Speed Laser Cladding Process
itself can be significantly influenced by the following varying parameters:
- laser power
- speed and concentricity
- Powder feeding
The ultrasonic welding process
can be significantly influenced by the following varying parameters:
- Amplitude and frequency
- Welding and holding time
- Material and surface finish
optimize your processes
weldmetrix GmbH
elevating standards, monitoring success
Headquarter
Gutheil Schoder Gasse 17
Techpark Vienna
1230 Vienna
Austria
Copyright © 2023 – weldmetrix GmbH