Cladding
What is the process
of laser cladding?
High-speed laser cladding is an advanced surface engineering technique where materials such as powder or wire are deposited onto a substrate using a laser as a heat source. This process creates a metallurgical bond with the surface, significantly enhancing the wear resistance, corrosion protection, and thermal stability of the components.
By using specialized materials and operating at high speeds of up to 400 meters per minute, laser cladding meets the high demands of modern production environments, such as those required in the automotive industry, especially in light of Euro 7 standards.
A great benefit of weldmetrix is its ability to organize, correlate, and integrate data seamlessly.
This gives companies a significant advantage by enabling real-time process monitoring and data analysis, improving production quality and maximizing uptime without interrupting workflow.
Laser cladding is particularly beneficial in applications that require precise and robust surface coatings, such as for brakes and engine components, which can last up to 300% longer and significantly reduce maintenance costs.
kW Laser Power
mm layer thickness
kg/hr deposition Rate
%
material utilization
Where is it used?
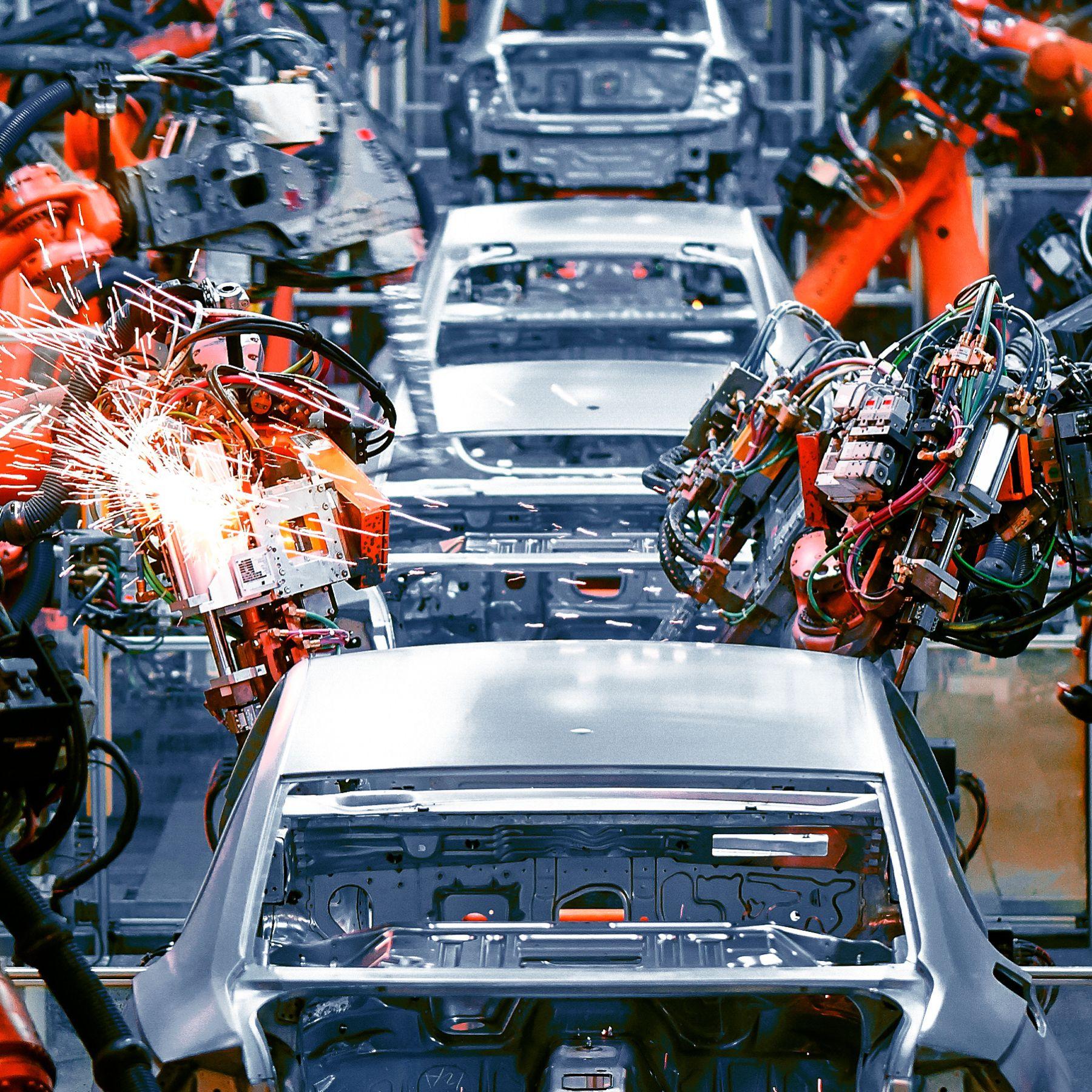
Automotive
Improves the durability of brake discs and high-wear engine parts.
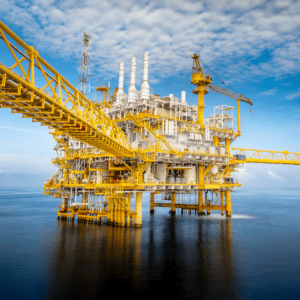
Oil and Gas
Protects drilling equipment from wear and corrosion, particularly under harsh conditions.
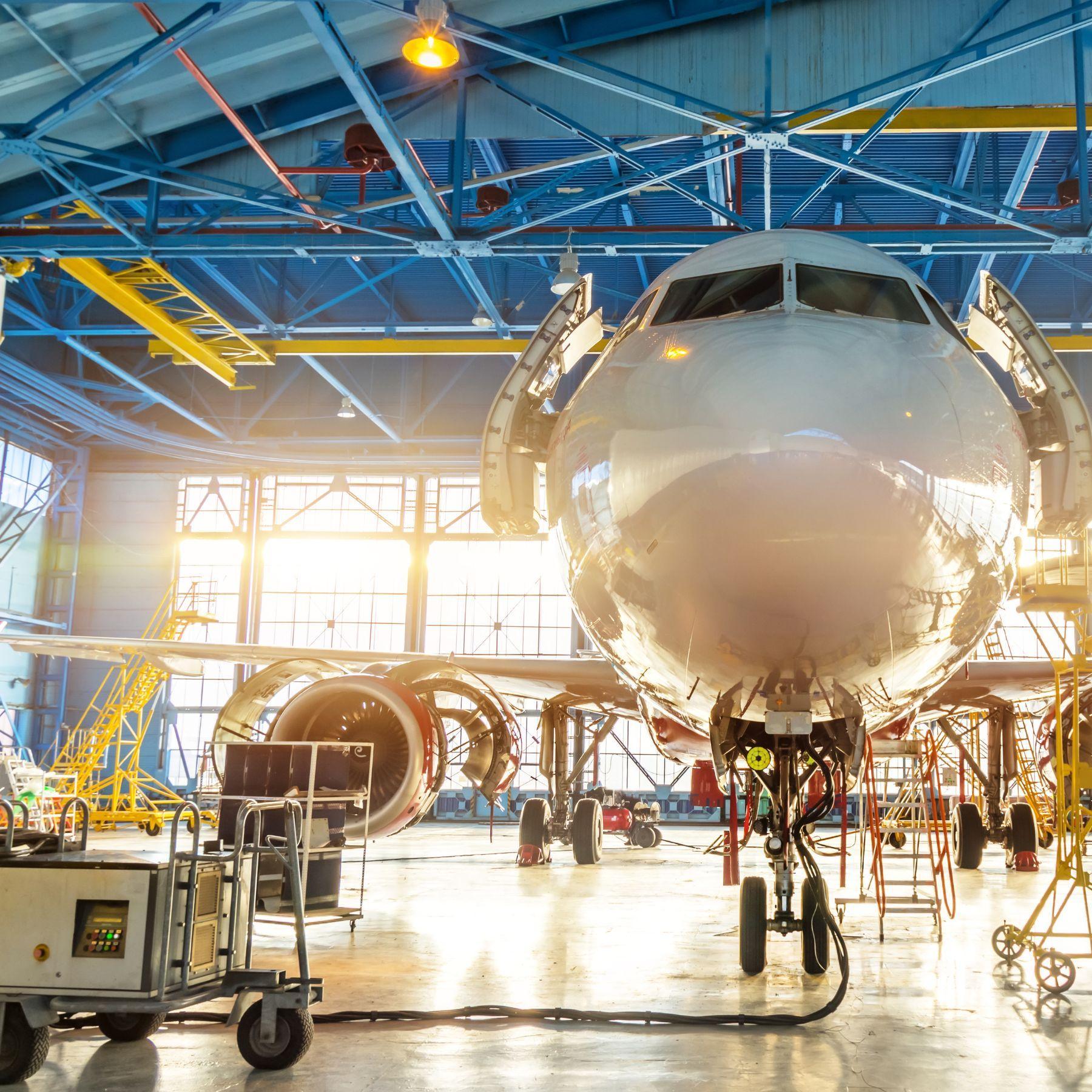
Aerospace
Repairs turbine blades and high-temperature components.
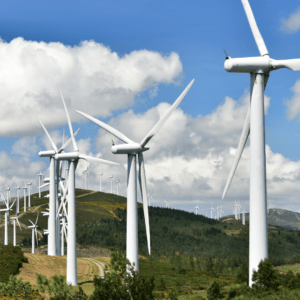
Power Generation
Extends the service life of turbine blades by adding corrosion- and heat-resistant layers.
Laser Cladding in brake disc production
A key automotive application is the cladding of brake discs. This significantly boosts their resistance to wear, extending their lifespan by up to 300%, thus reducing maintenance costs and downtime. The goal is to have one brake disc over a whole vehicles life time.
Laser cladding achieves a cladding speed of up to 400 meters per minute, ensuring production efficiency without compromising on quality. The process allows for high-precision layer thickness control, with a tolerance of up to ±5 micrometers, maintaining high performance under extreme stress.
Additional technical benefits:
- Layer Thickness: Achieved within ±5 micrometers tolerance for superior consistency.
- Speed: 400 m/min, leading to increased throughput and cost efficiency.
Other Applications Laser cladding is also essential for components like sliding bearings and shafts, where resistance to friction is critical. In sliding bearings, cladding can increase durability by up to 250%.
read more
With deposition rates up to 3 kg/hour, the process ensures efficient production with consistent layer thickness accuracy of ±5 μm, reducing overall operational costs.
Critical Process Monitoring: Layer Thickness and Distortion Measurement
For optimal results, layer thickness and distortion measurement are monitored continuously.
Using capacitive displacement sensors, real-time monitoring ensures uniformity and precision in layer thickness, essential for ensuring the desired wear resistance and corrosion protection. This is particularly critical in applications like brake discs and bearings, where deviations as small as a few micrometers can significantly affect performance.
Distortion Measurement: Real-time distortion monitoring prevents any warping of components due to thermal stress during the cladding process, which is especially crucial in aerospace applications where precision is non-negotiable.
Why is this important?
With the implementation of Euro 7 standards, the demands on components in the automotive industry are becoming increasingly stringent. These new regulations aim to drastically reduce emissions of nitrogen oxides (NOx) and particulates, while also requiring higher durability and resilience from parts.
Laser cladding helps extend the service life of critical components like brakes and engine parts to ensure they meet emission standards. By using this technology, companies can ensure that their components are long-lasting and reliable, even under the toughest conditions.
Moreover, studies such as the one from PwC have shown that the digitization and implementation of process monitoring systems can reduce production costs by 10-20%, increase production efficiency by up to 25%, and reduce scrap rates by up to 50%.
However, 40% of companies struggle with the implementation of such systems, often leading to high costs due to a lack of expertise. weldmetrix addresses this challenge by offering comprehensive training and support to ensure that our customers fully utilize the potential of the systems.
What does weldmetrix offer?
weldmetrix has revolutionized process monitoring for laser cladding by enabling high-speed processing of up to 400 meters per minute, with real-time data collection at a sampling rate of 1 MHz. This ensures even at such high speeds, no detail is missed.
Our core offering focuses on providing industry-approved solutions designed for series production environments. At weldmetrix, we offer much more than just a sensor. Our Center Unit and PROMOS software platform deliver a comprehensive solution for organizing, analyzing, and visualizing all relevant process data.
The dashboard enables real-time monitoring and central analysis of all sensor data, ensuring that all data is correctly captured and processed. This is especially crucial because improper use of the system can result in inaccurate data and inefficient processes.
In laser cladding, minute deviations in layer thickness or heat distribution can lead to component failure. Continuous monitoring ensures that every aspect of the process, from laser power to material feed, remains within optimal parameters.
read more
This guarantees that each component meets the stringent requirements of industries such as aerospace, automotive, and oil and gas, where failure is not an option.
In conclusion, laser cladding is a transformative surface engineering technique offering significant benefits, but its success depends on precise process control and monitoring. By integrating advanced technologies like weldmetrix’s real-time measurement systems, manufacturers can ensure superior quality, reliability, and efficiency in their cladding operations.
Studies show that 60% of companies that implement a process monitoring system later encounter problems because they do not fully understand or utilize the system. This is why it is so important for weldmetrix to focus on an easy-to-handle software system.
If not used correctly, every system can produce incorrect data, leading to costly production errors. Our sales trainers help customers unlock the full potential of the technology, ensuring that problems are avoided and the system delivers the expected results.
In the long run, our systems pay off: according to a McKinsey study, process monitoring systems typically pay for themselves within 12 to 24 months, provided they are used correctly. By combining efficient data utilization, qualified training, and robust solutions, weldmetrix ensures that the investment quickly becomes profitable by reducing costs, increasing efficiency, and lowering scrap rates.
weldmetrix GmbH
elevating standards, monitoring success
Headquarter
Gutheil Schoder Gasse 17
Techpark Vienna
1230 Vienna
Austria
Copyright © 2023 – weldmetrix GmbH