Ultraschallschweißen im Fokus:
Wie Weldmetrix die Qualitätssicherung revolutioniert
Willkommen in der Welt des Ultraschallschweißens, einem Bereich, in dem Präzision und Zuverlässigkeit nicht nur Wünsche, sondern Anforderungen sind. Hier kommt das akustische Überwachungssystem Weldmetrix MCRFN ins Spiel, das den emittierten Schall während des Schweißprozesses mit einer beeindruckenden Abtastrate von 50 kHz erfasst. Aber warum ist das so wichtig?
Das Prinzip des Systems ist einfach, aber wirkungsvoll: Wenn die Prozessparameter konstant bleiben, sind auch die Schallemissionen konstant. Änderungen der Schallemission sind ein untrügliches Zeichen für Unregelmäßigkeiten im Prozess. Mit Hilfe mathematischer Algorithmen wird das Geräuschverhalten analysiert und das System bewertet Fehler und Unregelmäßigkeiten entsprechend den parametrierten Anforderungen der jeweiligen Anwendung. Das heißt, je stabiler und reproduzierbarer der Prozess ist, desto genauer ist die Qualitätsbeurteilung.
In einem kürzlich durchgeführten Versuchsaufbau wurde eine Zwei-Kanal-Anwendung verwendet. Zwei Mikrofone des gleichen Typs wurden von unterschiedlichen Seiten und mit verschiedenen Anstellwinkeln positioniert. Interessanterweise wurden die Mikrofone mit einer Samplefrequenz von 50 kHz abgetastet, und die aufgenommenen Signale wurden unabhängig voneinander bewertet. Ein Verstärker und ein AD-Wandlungsmodul kamen ebenfalls zum Einsatz, und die gesamte Parametrierung und Visualisierung wurde über die Testsoftware auf dem Laptop eines Weldmetrix Technikers gesteuert.
Für die Tests wurde ein so genannter „High Runner“ verwendet, ein 5-poliger Stecker, der aus zwei Teilen besteht, die mit einer Branson 901 Ultraschallschweißmaschine verschweißt werden. Die Teile wurden manuell eingelegt, aber es ist geplant, diesen Schritt in einer späteren Serienanlage zu automatisieren. Die Tests selbst wurden mit dem Autotrigger des Weldmetrix-Systems durchgeführt, eine Funktion, die im Normalfall nur für Tests verwendet wird. In der Produktion wird ein digitaler Trigger verwendet, um sicherzustellen, dass alle Daten aufgezeichnet werden.
Das Weldmetrix MCRFN-System ist also nicht nur ein weiteres Tool im Werkzeugkasten der Qualitätssicherung. Es ist ein Paradigmenwechsel, der die Art und Weise, wie wir über Ultraschallschweißen und Qualitätssicherung denken, grundlegend verändert.
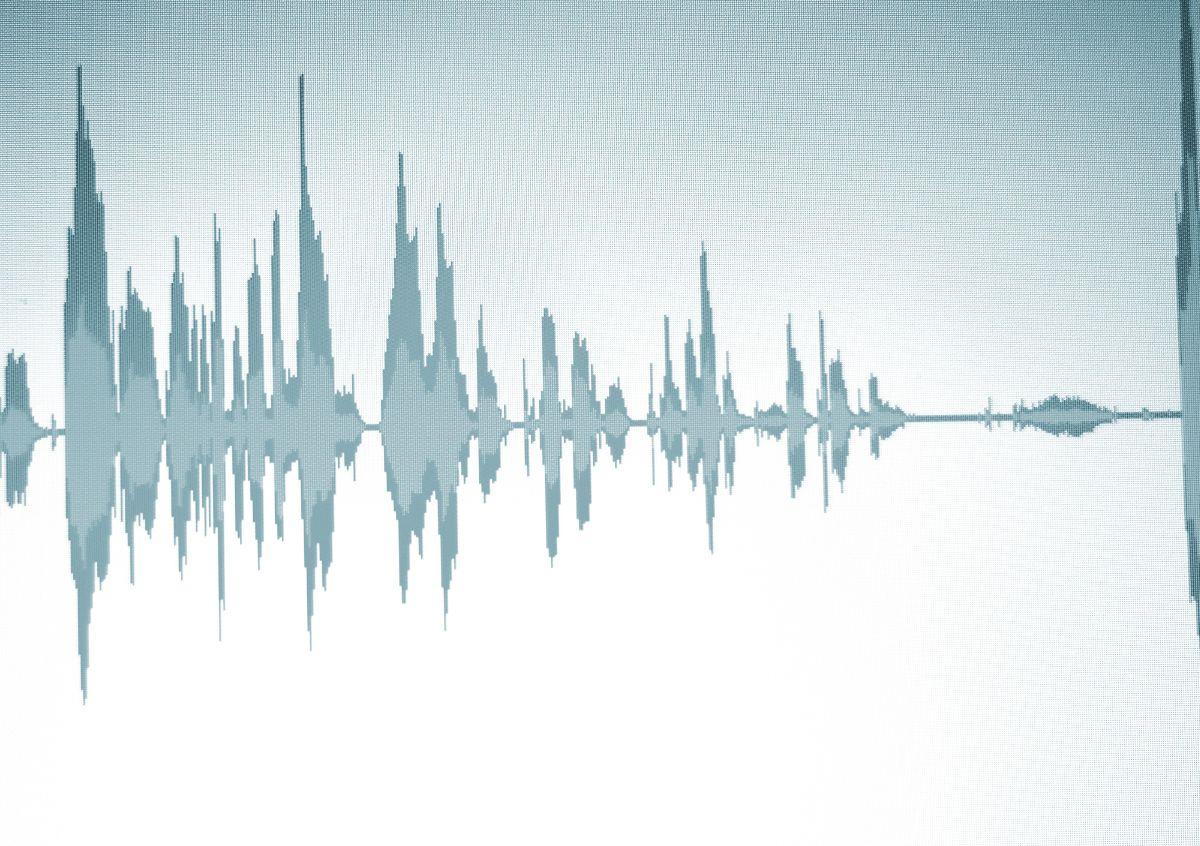
Versuchsergebnisse: Ein Blick hinter die Kulissen
Die Versuchsreihe mit dem Weldmetrix-System hat zu einigen bemerkenswerten Ergebnissen geführt. Zunächst muss betont werden, dass Weldmetrix ein vergleichendes und kein messendes System ist. Zu Beginn wurden Referenznähte IO (In Ordnung) geschweißt, um eine Basis für die Bewertung zu schaffen. Anschließend wurden NIO-Teile (Nicht in Ordnung) erzeugt, indem die Prozessparameter so verändert wurden, dass die resultierenden Bauteile die Mindestbruchkraft von 450 N nicht erreichten.
Interessanterweise zeigte die Auswertung, dass eine Veränderung der Prozessparameter nicht zwangsläufig zu einem NIO-Bauteil führt. Das Weldmetrix-System erkannte diese Änderungen in vielen Fällen korrekt, auch wenn das Bauteil den Zerstörungs-Test bestanden hatte. Für die Parametrisierung wurden alle Referenznähte als IO und alle provozierten Prüfteile als NIO deklariert. Die automatisch gesetzten Grenzen erwiesen sich als sehr zuverlässig.
Ein Sonderfall war das Bauteil 27, das als NIO bewertet wurde. Bei diesem Bauteil lag das Signal des Kanals 0 im letzten Teil der Naht bei allen vier Algorithmen über den Grenzwerten. Im Gegensatz dazu wurde das Bauteil 47 als IO bewertet, obwohl der Autotrigger nicht korrekt funktionierte und der Signalanfang nicht aufgezeichnet wurde.
Ein weiteres interessantes Beispiel ist das Bauteil 91, das eine unterdurchschnittliche Bruchkraft aufwies. In den Diagrammen ist deutlich zu erkennen, dass diese Messung deutlich länger ist als die Referenzsignale.
Insgesamt wurden fünf Bauteile ohne Folie geschweißt. Davon wurden vier als IO und eines als NIO bewertet. Diese Ergebnisse unterstreichen die Fähigkeit des Weldmetrix-Systems, auch subtile Veränderungen der Prozessparameter zu erkennen und korrekt zu bewerten.
Die Versuchsreihe hat somit nicht nur die Zuverlässigkeit des Weldmetrix-Systems bestätigt, sondern auch seine Fähigkeit demonstriert, ein breites Spektrum von Prozessvariablen zu berücksichtigen. Dies ist ein weiterer Schritt auf dem Weg zu einer noch genaueren und zuverlässigeren Qualitätssicherung beim Ultraschallschweißen.
Fazit: Die Kunst des richtigen Winkels und die Zuverlässigkeit des Weldmetrix-Systems
Die Versuche haben eindrucksvoll gezeigt, dass der Anstellwinkel des Mikrofons nicht nur eine untergeordnete, sondern eine entscheidende Rolle für die Qualität der Signalverarbeitung spielt. Ein größerer Anstellwinkel (CH0) ermöglicht zwar die Detektion eines breiteren Fehlerspektrums, hat aber auch seine Grenzen. Daher ist die Kombination von zwei verschiedenen Anstellwinkeln nicht nur eine gute Idee, sondern fast ein Muss, um das volle Potenzial des Systems auszuschöpfen.
Was die Parametrisierung betrifft, so wurden für die automatische Grenzziehung ausschließlich IO-Referenznähte verwendet. Dies erwies sich als kluger Schachzug, da alle Bauteile mit unzureichender oder unterdurchschnittlicher Bruchkraft vom Weldmetrix-System sicher erkannt wurden. Die Messungen, die trotz veränderter Prozessparameter standhielten, wurden bewusst nicht für die Parametrisierung verwendet. Dies unterstreicht die Genauigkeit und Zuverlässigkeit des Systems.
Insgesamt bestätigen die Ergebnisse die hervorragende Fähigkeit des Weldmetrix Systems, eine Vielzahl von Fehlern und Unregelmäßigkeiten sicher zu detektieren. Dies ist ein weiterer Meilenstein auf dem Weg zu einer noch effizienteren und zuverlässigeren Qualitätssicherung beim Ultraschallschweißen. Die Reise geht weiter und man darf gespannt sein, welche Innovationen als Nächstes auf uns warten.
weldmetrix GmbH
elevating standards, monitoring success
Headquarter
Gutheil Schoder Gasse 17
Techpark Vienna
1230 Vienna
Austria
Copyright © 2023 – weldmetrix GmbH